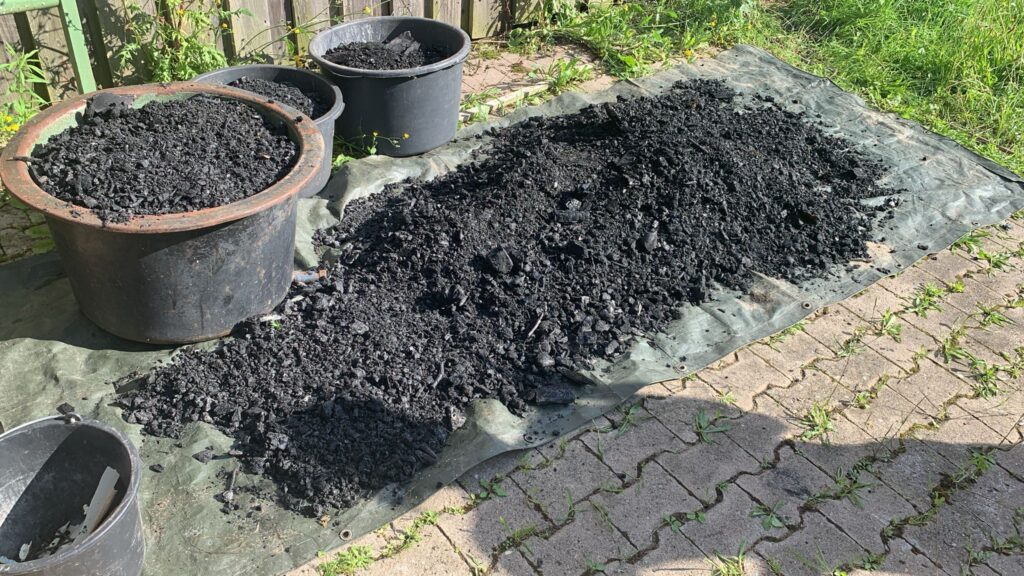
Introduction to the Next Phase of Water Filtration Prototyping by the JJS Foundation
At the New World Garden in Lower Saxony, our prototyping of rainwater filtration has reached a pivotal stage. Thus far, the system has successfully utilized only sand and gravel layers to pre-filter rainwater, which is further enhanced through regular movement and oxygenation. This initial foundational phase has established a solid basis for water quality improvement. We are targeting essential applications such as showering and drinking, which means we must go beyond semi-clean water and arrive at certifiably clean water. The water is already coming out taste and smell free, indicating that our low-tech sand and gravel filter is already doing a great job at removing fine particles and reducing the turbidity. Now we will take the next step shortly. BioChar will now be added to enhance the filtering process – following the methods recommended and thoroughly tested by Water Filtration expert, Dr. Joshua Kearns. Our system expands upon Dr. Kearn’s work in that we are introducing phytoremediation and continuous circulation of the water. This will lead to an integrated closed loop water system at the New World Garden, which is recycling only rain water – to produce a continuous supply of shower and drinking water.
As we advance to the next phase of our system prototyping, the focus is now shifting towards integrating activated charcoal, or BioChar into the filtration process. Charcoal, known for its exceptional adsorption properties, will be introduced in easy-to-maintain bags to enhance the removal of organic contaminants, odors, and residual chemicals from the water. The introduction of charcoal represents a significant upgrade, aiming to further purify the rainwater and ensure it meets high standards for safety and clarity. the charcoal will need to be replaced occassionally – and therefore bags will be used to make exchange of charcoal easier in roughly 12 months.
Key considerations for this phase include the preparation and maintenance of the charcoal bags. The size of the charcoal particles and the design of the bags will be critical factors in optimizing filtration efficiency. The charcoal needs to be processed to a suitable size to balance effective adsorption with manageable maintenance. Additionally, the maintenance protocol for these bags must be clearly defined to ensure consistent performance and water quality. These open questions will be addressed in the subsequent sections of the report, providing a comprehensive guide to implementing and managing the charcoal filtration stage effectively.
Effective Charcoal Filtration
Charcoal is a widely used medium in water filtration systems due to its high adsorption capacity, which helps remove contaminants and impurities from water. When integrating charcoal into filtration systems, the choice of containment bags and the maintenance practices are crucial for ensuring effective filtration and longevity of the system. This essay explores the optimal use of charcoal in combination with polypropylene bags, details the appropriate charcoal grain size, and discusses factors affecting charcoal quality, including contaminants like nails or partially burnt charcoal. Recommendations for maintenance are provided to ensure efficient management and annual replacement.
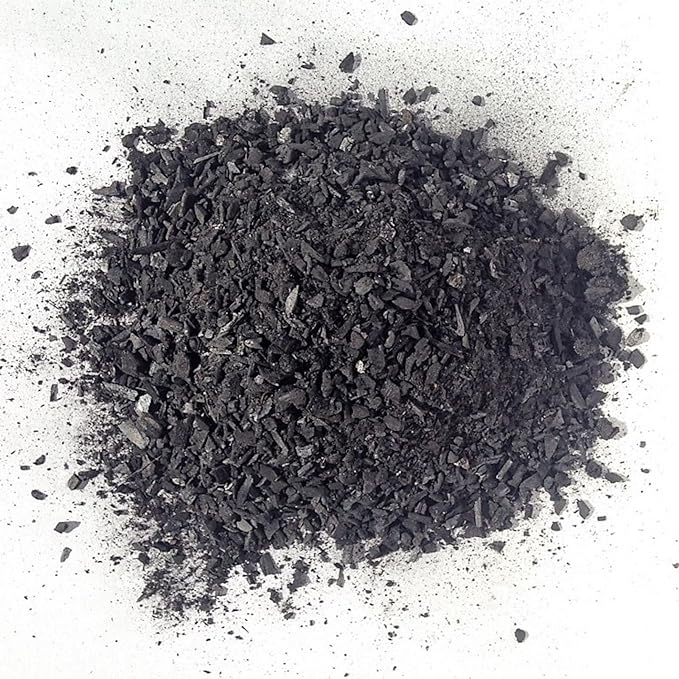
Charcoal and Bag Selection
1. Charcoal Size
The size of the charcoal used in filtration systems significantly affects its performance. The ideal size balances adsorption capacity with practical considerations like flow rate and maintenance. The commonly recommended sizes for charcoal in filtration systems are:
- 3 mm Charcoal: Offers a higher surface area relative to its volume, enhancing its adsorption capacity for capturing fine contaminants. However, it is more prone to clogging and may require more frequent maintenance. Smaller particles can also lead to a higher pressure drop across the filter.
- 6 mm Charcoal: Provides a better flow rate with less resistance and reduced clogging risk. It has a lower surface area compared to smaller particles, which might reduce its effectiveness in capturing finer contaminants but ensures less frequent maintenance.
For most practical applications, a charcoal grain size of 4 mm to 6 mm strikes a good balance, providing efficient filtration while maintaining manageable flow rates and reducing clogging.
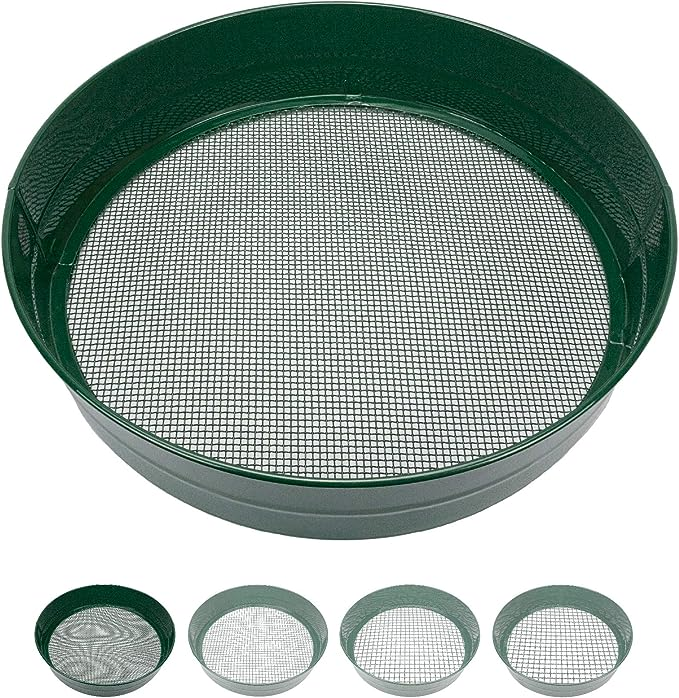
2. Charcoal Quality and Impurities
The quality of charcoal directly impacts the effectiveness of the filtration system. Key factors to consider include:
- Nails and Foreign Materials: The presence of nails or other foreign materials in charcoal can significantly affect water quality. Nails can lead to metal contamination, which might pose health risks if ingested. Additionally, foreign materials can cause physical damage to the filtration system or interfere with its operation. It is crucial to use charcoal that is free from contaminants and has been properly processed and cleaned.
- Partially Burnt Charcoal: Charcoal that is only partially burnt or contains uncharred materials may have reduced adsorption capacity. Partially burnt charcoal may also contain residues from the burning process, which can leach into the water and potentially introduce harmful substances. Ensuring that the charcoal is fully carbonized and free from residual contaminants is essential for maintaining high water quality.
3. Bag Material
Having examined cotton, nylon, polypropylene, and other options – we have chosen to work with polypropylene bags which are strong, resistant to rapid deterioration, and which are not likely to hinder water quality at all, while also allowing adequate flow through the bag’s pores.
Polypropylene Bags: Polypropylene is a popular choice for filter bags due to its durability and resistance to environmental factors. It offers several advantages:
- Strength and Durability: Polypropylene is strong and resistant to tearing and puncturing, which is essential for holding charcoal and withstanding the pressure of water flow.
- Weather Resistance: It withstands moisture, UV exposure, and extreme temperatures, making it suitable for various environmental conditions.
- Cost-Effectiveness: Polypropylene bags are generally affordable and widely available, making them a practical choice for many filtration systems.
4. Bag Design and Construction
The effectiveness of polypropylene bags depends on their construction and design:
- Mesh Size: Choose a mesh size that allows water flow while retaining charcoal particles. Common mesh sizes range from coarse to fine, depending on the filtration needs.
- Reinforcement: Bags with reinforced seams and high-quality stitching will be more durable and better suited for long-term use.
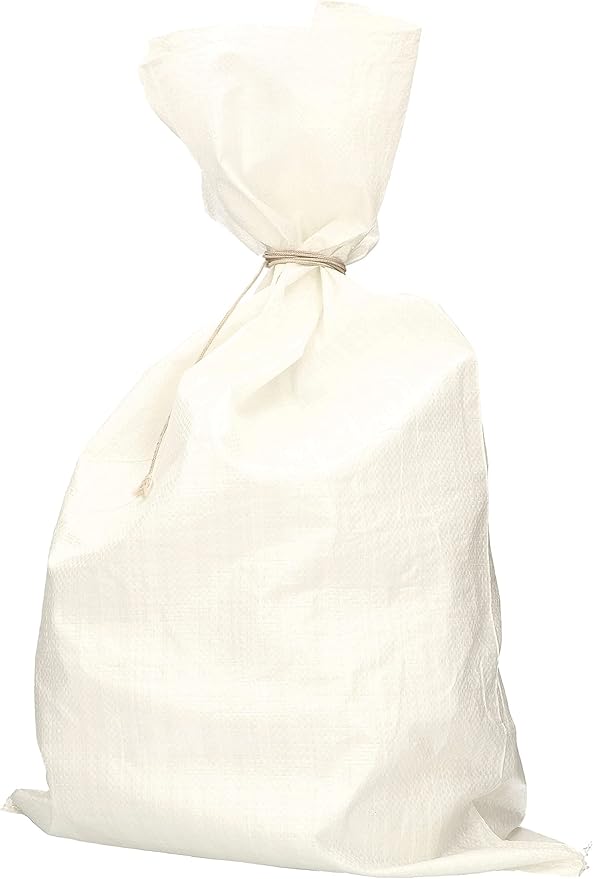
Maintenance Practices
1. Regular Inspection
To ensure optimal performance and longevity of both the charcoal and the polypropylene bags, regular inspection is crucial:
- Check for Physical Damage: Regularly inspect the bags for signs of wear, fraying, or damage. Damaged bags should be replaced promptly to prevent contamination.
- Monitor Flow Rate: A decrease in flow rate may indicate clogging or degradation of the bags. Address any issues promptly to avoid system inefficiency.
2. Cleaning and Replacement
- Charcoal Replacement: Charcoal generally needs replacement when it becomes saturated with contaminants or loses its adsorption capacity. For most systems, replacing charcoal every 6 to 12 months is recommended. If the bags are reusable, they should be cleaned thoroughly before reusing or replaced if they show signs of significant wear.
- Bag Maintenance: While polypropylene bags are durable, they should still be cleaned periodically if the design allows for it. Ensure bags are free from debris and contaminants that might affect their performance.
3. Best Practices for Longevity
- Pre-Filtration: Implement pre-filters to reduce the load on the primary charcoal bags. This helps in extending the life of both the charcoal and the bags by reducing the amount of particulate matter that enters the main filtration system.
- Storage: Store unused polypropylene bags and charcoal in a dry, protected area to prevent degradation from moisture or UV exposure.
Quality Concerns and Their Impact
1. Impact of Contaminants in Charcoal
- Nails and Metals: The presence of nails or metal fragments in charcoal can pose serious risks. Metals can leach into the water, potentially causing health issues such as heavy metal poisoning. Using charcoal that is free from metal contaminants is crucial for maintaining safe water quality (Huang et al., 2009).
- Partially Burnt Charcoal: Charcoal that is not fully carbonized may release residues from the burning process, which could include tar or other chemicals. These residues can contaminate water, affecting its taste, odor, and safety. Fully carbonized charcoal with minimal impurities is essential for effective and safe water filtration (Guo & Lua, 2002).
2. Best Practices for Charcoal Quality
- Source Quality Charcoal: Purchase charcoal from reputable suppliers who guarantee the quality and purity of their products. Charcoal should be properly processed and tested to ensure it meets safety and performance standards.
- Inspection of Charcoal: Inspect charcoal before use to ensure it is free from foreign materials and fully carbonized. Reject any batches that contain visible impurities or signs of incomplete burning.
Recommendations
- Charcoal Size: Use charcoal with a grain size of 4 mm to 6 mm for a balance between effective filtration and manageable maintenance.
- Charcoal Quality: Ensure charcoal is free from contaminants such as nails or metal fragments and is fully carbonized. Use high-quality charcoal to avoid issues with water quality.
- Bag Material: Employ high-quality polypropylene bags due to their durability, weather resistance, and cost-effectiveness. Ensure the bags have appropriate mesh size and reinforcement.
- Maintenance Schedule:
- Charcoal: Replace charcoal every 6 to 12 months, depending on usage and water quality. Regularly monitor the effectiveness of the charcoal and replace it if it shows signs of saturation.
- Bags: Inspect polypropylene bags every few months and replace them annually or sooner if they show significant wear or damage. Clean bags if they are designed to be reusable and if there are no signs of significant degradation.
- Pre-Filtration and Inspection: Implement pre-filtration and establish a routine for inspecting and maintaining the filtration system. This ensures efficient operation and extends the lifespan of both the charcoal and the bags.
Conclusion
Using charcoal in combination with polypropylene bags can be highly effective for water filtration systems if proper care is taken in selecting the appropriate charcoal size, ensuring high charcoal quality, and maintaining the bags. Regular inspection and timely replacement of charcoal and bags are key to managing the system’s performance and achieving long-term success. Ensuring the charcoal is free from contaminants and fully carbonized will help maintain high water quality and system efficiency.
References
- Guo, J., & Lua, A. C. (2002). “Preparation and characterization of activated carbons from palm shell by chemical activation.” Carbon, 40(2), 109-114.
- Huang, S., Huang, X., & Yang, Q. (2009). “Influence of Metal Contaminants on Activated Carbon Adsorption.” Journal of Hazardous Materials, 162(1), 103-112.